RFF’s Jay Bartlett and Alan Krupnick assess when and how “green” hydrogen—which is produced from water electrolysis using renewable or nuclear power—could be a valuable use of zero-carbon electricity.
This article is part of a series in which we expound on a recent report and explore how decarbonized hydrogen compares to other options for reducing carbon emissions—namely, carbon capture, utilization, and storage (CCUS) and electrification with zero-carbon power. By evaluating decarbonized hydrogen against these other two options, we explore when, where, and how hydrogen is likely to be a cost-effective method for reducing CO₂ emissions. A previous blog post compared blue hydrogen with CCUS, and subsequent articles will consider technology options and effective policy mechanisms for decarbonizing the power and industrial sectors.
While blue hydrogen, which we discuss in a previous blog post, is produced from fossil fuels, green hydrogen’s energy input (renewable or nuclear power) is already decarbonized. Therefore, it is not obvious why the production of green hydrogen would be worthwhile. The motivations for producing green hydrogen relate to three main advantages: it can provide cheap long-term storage, be used in combustion heating, and serve as a zero-carbon feedstock for industrial processes. As we’ll discuss, there are costs and benefits to each of these uses of green hydrogen. Figure 1 illustrates the first two uses, showing the pathways from renewable or nuclear power to energy storage or heat, with and without green hydrogen.
Figure 1. Energy Storage and Heat, with and without Green Hydrogen
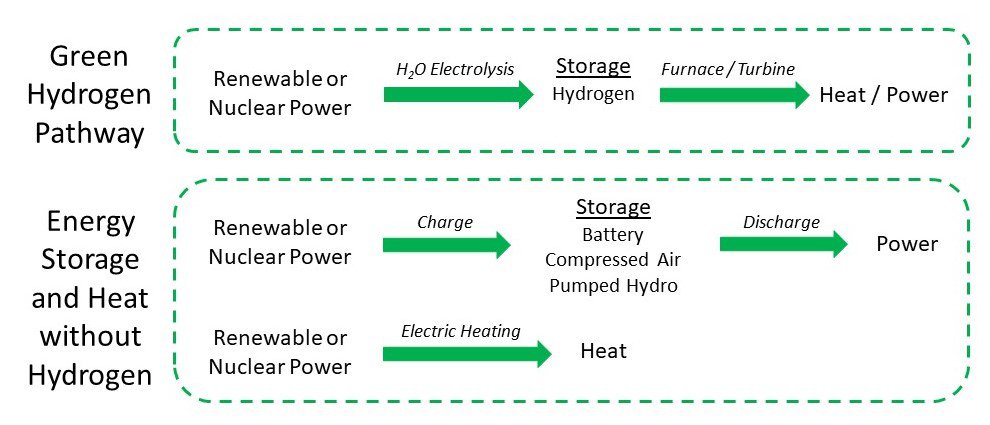
Turning first to energy storage: The costs of producing, storing, and utilizing green hydrogen are substantial. Energy is lost in converting power to hydrogen, compressing hydrogen for storage, and generating power from hydrogen combustion. Altogether, the round-trip energy efficiency of hydrogen-based storage is just 20 to 40 percent, depending on technology choices. In contrast, the round-trip efficiencies are over 90 percent for lithium-ion batteries, 80 percent for pumped hydroelectric storage, and 60 percent for compressed air storage.
However, hydrogen can be stored over time comparatively cheaply, so with longer discharge durations, hydrogen-based storage becomes more competitive. An analysis from the International Energy Agency finds that, for discharge durations longer than one or two days, hydrogen is the least expensive option for energy storage.
Turning next to providing heat: Green hydrogen converts zero-carbon electricity to a combustible fuel. From Figure 1, one might wonder how hydrogen-based heat could be preferable to simply using renewable or nuclear power for heat. Indeed, the green hydrogen pathway entails capital costs and energy losses for electrolysis and storage that do not exist for electric heating.
The rationale for green hydrogen is that heating for the industrial sector has particular requirements that electricity may not meet. Industrial heat typically is used to melt or vaporize materials or facilitate chemical reactions. Electric heating can reach high temperatures, but it may not be able to uniformly heat across all the necessary components. For example, heating a cement kiln internally with fuel combustion may achieve a more consistent temperature than heating the kiln’s external surface with electrical resistance. Even for industrial processes that can be redesigned for electric heating, the retrofits would necessitate significant capital expenditures. Furthermore, renewable power usually is intermittent, which is generally incompatible with industrial production. Therefore, green hydrogen is a means of converting potentially intermittent zero-carbon power to a continuous energy source that can be used more effectively and readily for industrial heating.
Turning to hydrogen as an industrial feedstock: The predominant way hydrogen currently is used is in oil refining and ammonia production (rather than combustion for heat or power). Producing green hydrogen thus creates a valuable zero-carbon material, which could displace high-carbon hydrogen in its current applications. Moreover, new applications—such as novel processes for iron and steel production—could use green hydrogen in place of natural gas or coal feedstock.
Having compared green hydrogen with renewable and nuclear power to assess its potential (and having done the same with blue hydrogen and CCUS), we will turn in subsequent blogs to the end-use sectors: industrial feedstock, industrial heat, and power generation. Although we have discussed applications of blue and green hydrogen in these sectors, we have not yet compared blue hydrogen to green hydrogen or, for example, green hydrogen to end-use CCUS. Notably, our discussion of hydrogen’s cost-effectiveness relative to a broader set of low-carbon options will go beyond our considerations so far of the incremental costs of decarbonized hydrogen versus zero-carbon power (for green hydrogen) or end-use CCUS (for blue hydrogen); instead, we will also evaluate the absolute costs of producing and delivering blue and green hydrogen.

Read more articles from the “Potential of Hydrogen for Decarbonization” blog series:
- “Evaluating Low-Carbon “Blue” Hydrogen Against End-Use CCUS” (January 11, 2021)
- “Reducing Emissions in Oil Refining and Ammonia Production” (February 4, 2021)
- “Reducing Emissions in Iron and Steel Production” (February 18, 2021)
- “The Right Policies Can Incentivize Cleaner “Blue” Hydrogen” (August 27, 2021)
- “Effective Incentives for Hydrogen Production, with Long- and Near-Term Climate Benefits” (November 15, 2021)